Collaborative robots have proven a very effective tool in helping manufacturers realize these goals in ways that make the bottom line sustainable as well.
Reducing waste with cobots
As part of its commitment to eliminate defects and waste during the manufacturing process, Italian power tool maker RUPES deployed UR robots to work alongside humans on production line assembly tasks.
The deployment resulted in reduced waste, lower operating costs, improved working conditions, allocation of workers to higher value tasks, and enhanced productivity.
Universal Robots’ commitment to the fact that Quality Matters provides significant reassurance for manufacturers concerned about the sustainability of their operations.
In addition, the UR+ ecosystem of UR-certified application kits and components provides a wide range of specialized industrial quality inspection systems that can be used to reduce waste and improve the quality of finished products.
Cobots reduce energy consumption through remote monitoring and access
Digitalization of manufacturing processes supports sustainability by reducing travel costs, optimizing energy consumption, and providing tools that manufacturers can use to streamline their automation deployment.
The UR+ ecosystem supports digitalization with a wide range of remote monitoring and access solutions.
Remote monitoring tools allow users to track and monitor cobot performance without having to go onsite.
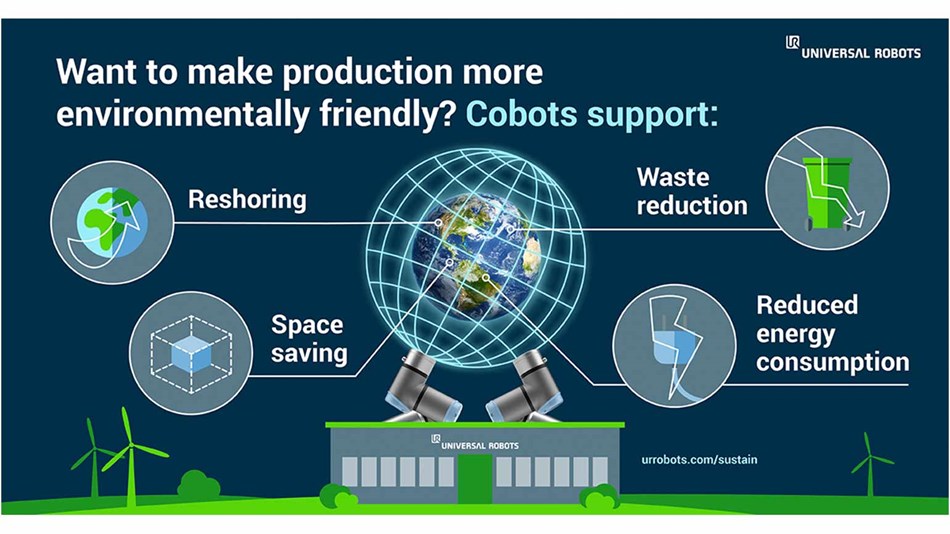
Typically accessible via tablet, PC and smartphone, these tools provide a wealth of information on KPIs that can then be used to tweak the cobots’ performance, resulting in improved production efficiency and reduced electricity consumption.
Remote access tools enable manufacturers to program their cobot(s) remotely, saving on travel costs and reducing the environmental impact of the automation deployment.
Environmentally friendly footprints
Traditional automation typically comes with a large footprint and usually necessitates significant changes to the layout of the production facility. In some cases, new construction is required to create space for the robot.
In contrast, UR’s lightweight cobots have a small footprint and based on the risk assessment, most cobots require no safety guarding, making them easy to move between applications while eliminating costly facility redesigns.
Maximizing energy-efficiency in cobot deployments
Generally speaking, cobots are more affordable and consume less energy than their traditional robot counterparts.
There are very simple steps manufacturers can take to minimize energy consumption in their cobot-powered applications; running your cobot at 70-80% of its maximum speed and payload, where possible, will reduce energy usage and extend the lifespan of the cobot.
And when it comes to application design, make sure to consider path optimization strategies as this will also reduce electricity consumption when the cobot is up and running.
Any thoughts?